In order to conserve water resources, we actively use rainwater. The Headquarters have been using rainwater since 1991, and various Group locations are also actively using rainwater. Moreover, Jiangsu Mabuchi and other Group locations have built wastewater treatment facilities at our factories, reusing some of the treated water for watering plants and toilets. We will continue to monitor the impact of our business on water and strive to protect water resources.
Efficient Use of Resources
Initiatives for Sound Water Management
Waste Reduction Initiatives
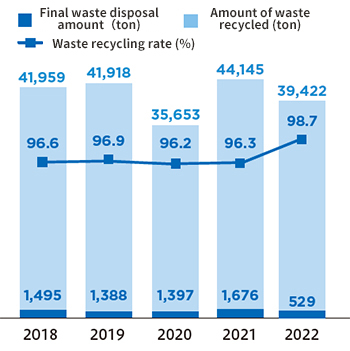
We set the target of recycling 95% or higher of the waste we generate, aiming to establish a recycling-oriented society where waste is collected and recycled as resources and the amount of waste disposed in landfills is minimized. To establish a recycling-oriented society, it is necessary to reuse waste as resources in addition to reducing waste. In addition to our current recycling rate, we started compiling our recycling rate when not including thermal recycling in 2023, and in order to improve that recycling rate, the Headquarters are working to reduce combustible materials as an environmental management system goal. The efforts to reduce and recycle waste will continue throughout the Mabuchi Group.
Waste reduction indicators and initiatives for 2023
[Target] Waste recycling rate: 95.0% or more
[Achievement] Waste recycling rate: 97.9% (achieved).
Thorough Separation
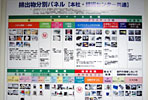
Separation of waste is essential for recycling. To promote thorough separation that is easy for everyone, we post signs on separation in prominent locations and establish places for people to leave wastes.
For disposal of motor materials as resources, parts are separated by type of material and processors are selected for each material. While we have contracts with two recycling companies in Japan, some materials at overseas factories cannot be recycled and we are trying to find processors for these.
Resource Recycling
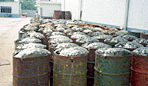
We use tens of thousands of tons of steel to manufacture motor housing (motor case) parts. The steel material is made into parts by press working through processes such as punching and drawing. From the viewpoint of efficient use of resources, we aimed to improve the material yield rate, minimized the punching width due to the difference in material thickness and material, and reviewed various processes such as feed accuracy in press working. As a result, the material yield rate has improved by 5%. In addition, 100% of the scraps generated during press working are reused.
Reuse of waste heat at overseas bases
The hot water supply system at Dalian Mabuchi and Wafangdian Mabuchi in China has been changed to a system that can recover and reuse exhaust heat. By using hot wastewater and air-conditioning exhaust heat, power consumption has been reduced by more than 80% compared to hot water supply using only electricity.
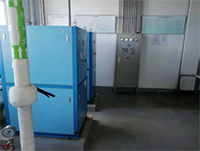
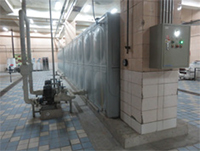
Efforts in Headquarters
Reuse of waste heat
Our Headquarters building was built based on Mabuchi Group's Basic Environmental Policy which aims to make the best use of limited resources. By adopting state-of-the-art technologies and methods such as a double-skin structure to minimize heat load and a building-frame thermal storage, the building is well equipped to allow proactive pursuit of energy savings and has achieved more than 20% reduction in life-cycle CO2 emissions compared with buildings of similar scale with standard facilities. emissions over the building's life cycle compared with those of standard facilities.
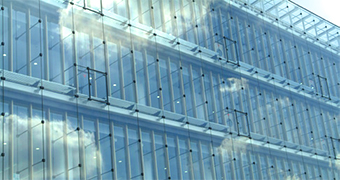
Environmental measures in the construction of the parking structure for employees
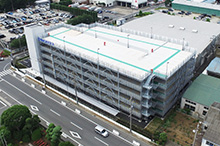
In the construction of a parking structure for the employees of Headquarters, we reduced about 8 tons of CO2 by using LED lights, of course, and also by reducing the use of wooden molds, scaffolds, and excavation soil as environmental measures in the construction phase.
Recycling of Waste
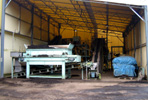
Since fiscal 2006, Headquarters has been working to recycle food waste, cultivating recyclable suppliers, and continuing to use food waste as feed and compost. As a result, 100% of the garbage generated at Headquarters can be recycled. In addition, 100% of the leaves and twigs on the premises of the head office are recycled by composting them.
Efforts in Factories
Reducing Waste in the Production Process
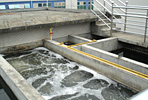
The tip of the motor shaft (*) is chamfered. We have reviewed the polishing method and switched to a forging method to reduce industrial waste and simplify wastewater treatment facilities.
- *Shaft : an important part that takes out rotation output from the motor and transmits the power to the unit.
Efforts in the Logistics Field
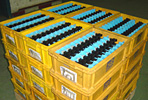
In the logistics field, we are working to reduce waste by promoting the recycling of polystyrene packing materials used to deliver products to customers and the use of reusable returnable boxes. In addition, in order to reduce the amount of CO2 generated during the collection and transportation of recycled packaging materials, we are promoting the construction of a collection processing system in Japan as well as in locations near our customers.