Basic Strategy
Our management principles are "contributing to international society and continuously increasing that contribution." We position the principles as the purpose of our presence as a company and are performing our corporate activities toward the achievement of the purpose. In developing our management strategy, our management principles are also regarded as the most important criteria.
Under these unchangeable management principles, without being preoccupied with short-term profits, we would like to develop and grow steadily into a company indispensable for society.
Specialization of Business Area
We are clearly limiting the scope of our products and technologies to that related to small DC motors. Some might think that this specialization in business related to small DC motors weakens corporate foundations. However, continuously improving and deepening the technologies widens the range of using small DC motors, and this allows more diversified applications of the motors.
As a result of focusing all of our management resources on core competence by always eyeing the global market, we have gained the largest share in the world in the small DC motor industry. Our world's largest production volume is proof of high evaluation and confidence we are receiving from our customers. On the other hand, however, we have a substantial social responsibility for continuously supplying high-quality products steadily.
"Standardization strategy" and "international specialization system" are our strategies for simultaneously achieving two opposing goals, namely, high quality and low cost.
Standardization Strategy
The following are descriptions of a historical background that has made us decide to start our standardization strategy:
Background of developing the strategy
In the toy industry, which was our core market at the time of our foundation, we used to perform make-to-order production meeting individual requests that varied depending on customers. Since motors had individual specifications, we were forced to perform high-mix low-volume production (limited production of diversified products) that resulted in high production cost.
Moreover, since most of the motors for toys produced at that time were incorporated in products for Christmas sales battles in Europe and the U.S., the production volume had extreme seasonal variations, and this made it difficult to secure employment and quality that were stable all the year around.
Since these problems became overt as the motor production volume rapidly increased, we were required to stop dealing with the make-to-order production, which was the root cause of these problems, and to moderate the seasonal variations.
Standardization of products
In order to solve the above problems, we have decided to manufacture standard motors, which cover as much similarities among various needs of our customers as possible, by summing up such needs. Narrowing down the models of our motors has allowed us to perform mass production and to equalize the production. This has stabilized both employment and quality, and has widely reduced cost compared with the cost required during the time when we had been dealing with the make-to-order production. Consequently, we could reduce our motor prices dramatically.
The reduction of motor cost has also contributed to expand our motor applications as a result of sustaining and expanding our price competitiveness in relevant markets and further upgrading our motor performance continuously. Thus, a virtuous cycle has been created, in which increase in customers to purchase our standard products allows further cost reduction due to economic effects of scale, and this has led to our success in maintaining sustained competitive superiority.
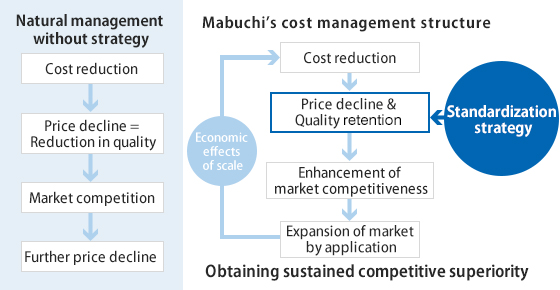
Standardization of production equipment, process, and administrative task
Standardization of products has also allowed standardization of production equipment and process that create the products.
To manufacture high-quality products utilizing many employees, it is essential to thoroughly provide operating instructions to the employees. Standardization of the equipment and process has allowed efficiently educating and training the employees and then speedily putting them to the process.
Our system, which is based on "standardization" and can produce stable-quality products without necessitating highly-skilled workers, has played a leading role in increasing the number of our overseas production bases.
In addition to this, standardization of administrative task has allowed scheduled production based on control by our Head Office. This has minimized impacts of seasonal variations or economic fluctuations by industry and has ensured stable supply of mass-produced products to relevant markets.
Additionally, based on our concept of expanding the versatility of products by maximally enhancing motor functions, we are making efforts not to lightly manufacture exclusive-use motors for particular applications. Therefore, currently we only have approximately 90 basic models.
Regardless of how thought-out a standard product may be, however, there is no certainty that the product remains effective in the future without upgrading the product. It is required to always understand market needs and to reflect the needs in the performance of the standard product. Customers require not a standard product but a low-price and high-quality motor meeting their needs. The major point of "the standardization strategy" is how to attract customers' demand to our standard products through maintaining cost competitiveness and finding out market needs.
International Specialization System
Another effort characterizing our strategy is the international specialization system.
Since the tenth year after our foundation, we have been selecting developing countries and areas, which have enabled us to utilize plentiful labor force inexpensive compared to that in Japan, have been boldly making inroads in the countries and areas, and have established overseas mass-production systems earlier than any of our competitive manufacturers.
Currently we have 19 overseas bases.
Pursuing the best balance between labor and machinery
In establishing any production base, we are aiming at achieving both high quality and low cost at a time not only by using inexpensive labor force but also by pursuing the best balance between labor and machinery.
The best balance here means to freely adopt advanced machine technologies for operations requiring high processing accuracy that is difficult to achieve manually, operations fraught with danger, or processing of precision parts in which difference in production scale significantly impacts on cost, and to actively utilize labor for processes such as motor assembly process that can secure required quality manually.
We believe that our efforts mentioned above hold down excess depreciation burdens and also lead to our social contribution in the form of expansion of job opportunities in our host countries.
Aiming at co-existence and co-prosperity with host countries
Starting with entering into Hong Kong in the tenth year after our foundation, we have been establishing production bases in various regions in Asia including Taiwan, China and Vietnam, and optimizing our motor production systems for our motors that are always competitive.
We believe that we have been contributing to our host countries' economic development since our entry into these developing countries and areas have promoted provision of job opportunities to and entry of other foreign companies into these countries and areas.
On the other hand, it may become impossible to perform labor-intensive production activities due to environmental changes such as increase in wages or labor shortages. Therefore, we are aiming at co-existence and co-prosperity of the entire Mabuchi Group with each of our overseas bases, eventually with our host countries, by changing roles of our bases from fixed ones to flexible ones, the quality of the roles is to be improved according to changes in the environment surrounding our bases, and according to growth in human resources and organizational power of our bases.